How HiveMQ and MQTT Support USCAR
The automotive industry is rapidly evolving, with smart manufacturing practices becoming essential for efficiency and competitiveness. The United States Council for Automotive Research (USCAR) plays a key role in promoting collaboration and standardization among major automakers through its USCAR-53 goals. However, manufacturers face challenges in data communication and interoperability, which are critical for meeting the USCAR standards, particularly USCAR-53.
In this blog post, we will walk you through how HiveMQ’s MQTT platform can help manufacturers tackle several data communication challenges and helps accelerate industrial data communication proposed by USCAR-53. Let’s dive in.
Introduction to United States Council for Automotive Research (USCAR)
USCAR is an automotive technology consortium made up of major US automotive companies Ford, General Motors, and Stellantis. Founded in 1992, USCAR facilitates the collaboration of its members to address pre-competitive challenges and opportunities in major automotive technology areas including advanced propulsion, electrical & electronics, energy storage, hydrogen fuel cells, manufacturing, materials, and safety.
Specifically for Automotive Manufacturing, USCAR created the USCAR-53 specification in collaboration with Michael King at our partner LHP Analytics & IoT, aimed at the creation of a universal methodology for data communication, machine language, and reporting to and from manufacturing devices in the smart manufacturing automotive production environment. They also collaborated with the Clean Energy and Smart Manufacturing Innovation Institute (CESMII) to develop a “Roadmap for Automotive Smart Manufacturing” for standards-based openness and interoperability of platforms and applications to enable a more productive, competitive and resilient automotive manufacturing environment in the U.S.
Challenges in Industrial Data Communication
In the manufacturing environment, some of the industrial data challenges include:
Stovepipe Architectures where data is trapped within various applications focused on specific manufacturing processes
Vendor Lock-ins due to many equipment vendors developing their own proprietary software that is incompatible with other vendors
Propriety, Closed Protocols created by vendors to restrict access to raw machine data in efforts to monetize access and promote vendor-specific analytics
Lack of Interoperability caused due to these proprietary protocols and vendor-specific software which blocks plug-and-play equipment deployments
No Application Portability because proprietary protocols require custom applications for each vendor, increasing costs and creating additional data silos
Data Silos caused because manufacturing data is trapped in factory-specific applications, minimizing the use of advanced analytics
Difficulty to Scale caused by legacy plant floor applications limiting the scale and speed of smart manufacturing deployments, driving up costs, and limiting the ability of IT staff to provide functional support/upgrades
Lack of cross-OEM Ownership which is an industry-wide issue that no one company by itself can solve
Overcoming these challenges will provide many advantages like reducing costs, maximizing scale, improving quality, reducing time to market, optimizing performance, enhancing security, reducing recruitment downtime, and many more.
One of the ways to overcome these challenges is to adopt Industrial Internet of Things (IIoT) open standards. The overarching goal of IIoT connectivity is to unlock data in isolated systems (“silos”) to enable data sharing and interoperability between previously closed components and subsystems (brownfield), and new applications (greenfield), within and across industries. One of the key IIoT message protocols being called out to be adopted by the manufacturing value chain in this specification to enable open-standards-based communication is MQTT.
Figure 1 – Data Communication Reference Architecture | Image Source: United States Council for Automotive Research (USCAR)
Fig. 1 above depicts an overarching future state for industrial data. The figure shows data flow to and from the Industrial Data Sources through the MQTT Broker, to and from the Smart Factory Solutions to be implemented.
How MQTT Enables Industrial Data Communication
MQTT is a lightweight publish/subscribe-based messaging open standard protocol used in IIoT for data communication and is designed for efficient communication between industrial data sources and smart factory solutions in low-bandwidth, high-latency, or unreliable networks. Instead of needing to set up direct communication as in the case of client server architectures, in MQTT architecture both publishing and subscribing clients communicate through a centralized server also known as a message broker (Fig. 2). This enables multiple enterprise systems to subscribe and ingest various manufacturing data via MQTT topics, and allows devices to publish data to a broker and applications to subscribe to that data. This also allows message payloads to be shared and consumed in JSON, XML, and other common formats.
Thus, MQTT can help address various IIoT data challenges by facilitating real-time data exchange, with high reliability and scalability. Figure 2 – MQTT the de facto IIoT data standard protocol
Unified Namespace (UNS)
In addition to providing the central hub for industrial data, MQTT also enables a data framework called Unified Namespace (UNS). UNS enables Industrial Machine communication best practices by providing the following:
The single source of truth for all data and information of the manufacturing operations
The place where the current state of the operation lives
The hub through which the smart devices in the company’s business communicate
The architectural foundation of the company’s Industry 4.0 and Digital Transformation initiative.
Figure 3 – Industrial Machine Communication Emerging Best Practice Architecture | Image Source: USCAR
As described in Fig. 3 above, the UNS is able to provide a contextualized view of all of the industrial data parts, machines, plant or environment whether they are job related or non job related (refer to Fig. 1). This could include, for example, part quality information, machine alarm state, machine sensor data values or plant configuration values. Instead of having to go to multiple systems to fetch this information, the UNS allows easy access to all of this information in one location.
HiveMQ: Accelerating the Industrial Data Communication Proposed by USCAR
HiveMQ is a proven enterprise MQTT platform that is reliable under real-world stress, is built for flexibility, security, and scale, and provides real-world solutions to support Smart Manufacturing data use cases.
Figure 4 – HiveMQ IIoT Enterprise Data Architecture for Smart Manufacturing
HiveMQ helps accelerate the industrial data communication standards that USCAR created and meets the requirements of the Automotive Manufacturing Industry in multiple ways:
Data Ingestion and Data Quality at the Edge
HiveMQ provides a HiveMQ Edge gateway that can translate device sensor data points in various formats like OPC UA, Modbus etc. into MQTT; store and forward the data if connection is lost; transform, normalize and contextualize the data through Data Hub so that it can all be interpreted easily and bridge to an enterprise broker. Data can be further consolidated, transformed and contextualized in the Enterprise MQTT broker using the Data Hub feature. This helps overcome the problems of stovepipe architectures, vendor lock-ins, and proprietary closed protocols enabling robust bidirectional communications between industrial data sources and smart factory solutions.
Reliability
HiveMQ supports MQTT’s three quality of service (QoS) levels to control whether a message is sent at most once, at least once, or exactly once. This makes it possible to establish reliability rules for various kinds of messages related to industrial data to be shared at various levels of reliability based on the use case. In addition to the standard reliability features offered by MQTT, HiveMQ offers additional reliability features like the following:
No single point of failure with a distributed and masterless cluster architecture, which means there is no single point of failure, and the cluster can grow and shrink at runtime without losing data or availability.
Zero message loss which includes persisting messages by storing them to disk, disk replication, and offline message queuing.
Reliable communication which includes automatic throttling as needed, to prevent cluster overload, dynamic queuing across clusters to ensure even load distribution, and retaining messages on disk.
Security
HiveMQ ensures the secure transfer of manufacturing device data with industry standards such as TLS, secure WebSockets, and state-of-the-art cipher suites. Support for authentication and authorization includes X.509 certs, username/password, IP-based authentication, and an API that allows for custom authentication, authorization, and permission logic, such as OAuth 2.0 integration. This ensures highly secure connections between sensors, PLCs, and controllers on the Operations Technology (OT) side and the Information Technology (IT) applications on the enterprise and cloud, like remote monitoring applications or prediction analytics or other Artificial Intelligence (AI) applications. The HiveMQ Enterprise Security Extension (ESE) makes it easy to integrate third-party enterprise security systems into HiveMQ, including support for authentication and authorization using SQL databases, OAuth 2.0, and LDAP. See Fig. 5 for more information.
Figure 5 – HiveMQ Security Architecture
Scalability
HiveMQ scales with underlying OT hardware. HiveMQ has benchmarked 200M concurrent connections while maintaining high-speed throughput and adding minimal latency. This is especially useful to ensure data is transferred quickly when plant floors have limited data connectivity and bandwidth. This helps address the problem of difficulty to scale caused by legacy plant floor applications.
UNS
HiveMQ supports the UNS framework by default by virtue of being an Enterprise MQTT platform. In addition to that, HiveMQ offers a number of features including HiveMQ Edge, Data Hub, Enterprise Broker and Extensions that helps provide a robust UNS experience to the manufacturing customer. This helps address the problem of the lack of cross OEM ownership, application portability, and interoperability issues identified by USCAR as impediments to robust industrial data communications.
Extension Framework
HiveMQ has an open API and flexible extension framework that enables integrating manufacturing-related data consolidated in the UNS into enterprise systems like stream application platforms, databases, and custom applications. The extension framework allows developers to quickly create extensions for custom data processing, device authentication, and device authorization mechanisms. HiveMQ also provides a marketplace of pre-built extensions for sharing IIoT data with Azure, AWS, Google, Kafka, MongoDB, and other systems.
Full Support of MQTT 5
HiveMQ provides full support for MQTT 5, the most recent version of the MQTT protocol. MQTT 5 includes new features that make it easier to develop reliable systems and integrate the industrial data into other systems.
HiveMQ is 100% compliant with all versions of the MQTT specification. MQTT 3 and MQTT 5 clients can communicate with HiveMQ simultaneously. All features, such as topic wildcards, persistent sessions with offline queuing, retained messages, and quality of service levels, are available at scale.
HiveMQ: Enabling the Promised USCAR Industrial Data Communication Standard
The USCAR-53 promise is to develop and deploy an Industrial Data Communication Standard that provides the foundation for smart manufacturing across the automotive manufacturing industry worldwide by the end of 2025. While there are still lingering data challenges in the industry, certainly MQTT and HiveMQ can help overcome these challenges and get the Automotive Manufacturing Industry OEMs and suppliers well on the path of compliance to USCAR-53.
To learn more about HiveMQ, download and try out the software for free or schedule a demo today.
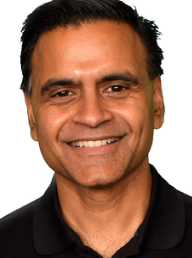
Ravi Subramanyan
Ravi Subramanyan, Director of Industry Solutions, Manufacturing at HiveMQ, has extensive experience delivering high-quality products and services that have generated revenues and cost savings of over $10B for companies such as Motorola, GE, Bosch, and Weir. Ravi has successfully launched products, established branding, and created product advertisements and marketing campaigns for global and regional business teams.