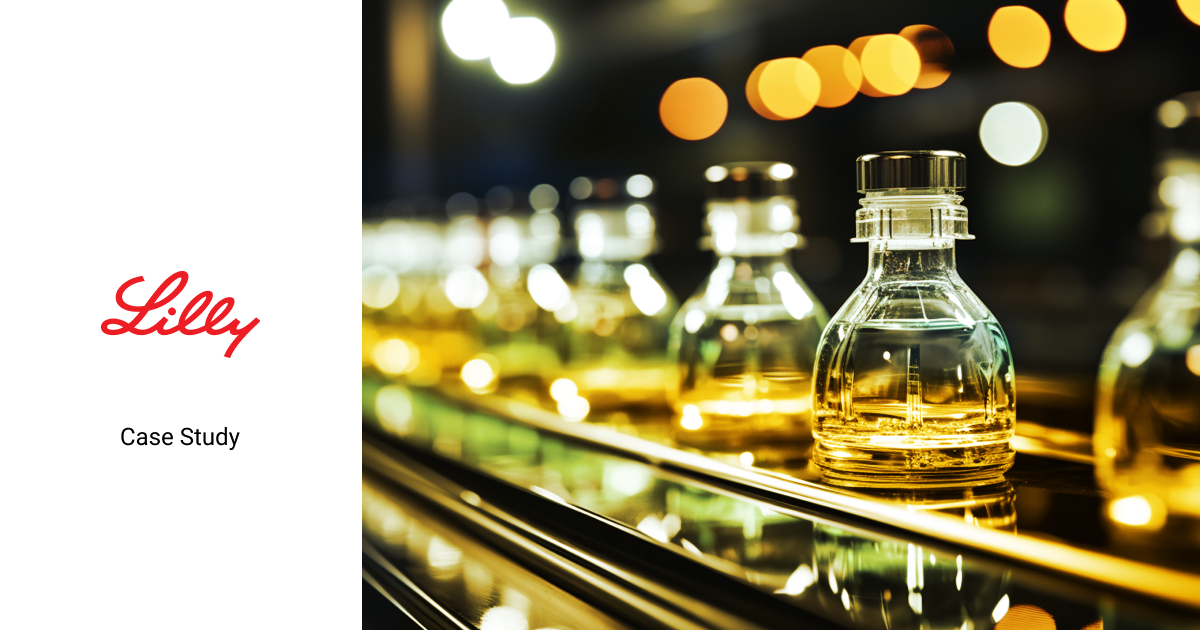
Savings Per Year by Reducing Energy Usage by 20%
Savings by Reducing Production Downtime by 40%
Savings Due to a 25% Improvement in Workforce Efficiency
Manufacturers face rising pressures from unplanned downtime, supply chain disruptions, increasing costs, and regulatory compliance. To stay competitive, they must improve efficiency, ensure quality, and accelerate time to market. Smart manufacturing leverages Industrial IoT (IIoT) technologies to enable real-time decision-making, predictive maintenance, automation, and resource optimization. By reducing downtime, enhancing agility, and ensuring compliance, manufacturers can lower costs, boost productivity, and deliver higher-quality products in a rapidly evolving marketplace.
HiveMQ is the enterprise MQTT platform that lays a powerful foundation for Industry 4.0. It solves data connectivity and interoperability challenges across a variety of manufacturing industries, including automotive, chemical, food and beverage, and pharmaceutical.
HiveMQ helps manufacturers unlock the power of their industrial data by enabling real-time, reliable, and scalable communication between machines, sensors, and enterprise systems.
Customers maximize asset utilization and reduce downtime with reliable, low-latency machine data, enabling predictive maintenance and real-time production optimizations.
Manufacturers eliminate defects and ensure consistency by applying real-time monitoring and automated alerts to detect and correct quality issues before they impact customers.
Companies streamline workflows and eliminate data silos by seamlessly integrating IT and OT systems, reducing inefficiencies and enabling intelligent automation.
Customers predict failures and optimize maintenance strategies by tracking Mean Time to Repair (MTTR) and Mean Time Between Failures (MTBF) in real time, reducing costly downtime.
HiveMQ has delivered the stability and reliability that we require for our system. We have been using HiveMQ for 4 years and the broker has not gone down. It is rock solid, completely reliable. This is very important since we can’t stop the factory assembly line.
Marius Hertfelder
/Mercedes Benz
Efficient data collection, communication, and control are key for smart manufacturing. HiveMQ provides a scalable, secure, and reliable data layer that ensures real-time, event-driven data exchange across OT and IT systems.
Zero message loss with persistence to disk and offline queuing
No single point of failure due to masterless cluster architecture and zero downtime upgrades
Elastic scaling with automatic data balancing and smart message distribution
Proven benchmark of up to 200M active clients with 1.8B messages/hour
Runs anywhere on premise or in public or private clouds
Efficiently connects to streaming applications, databases and data lakes with a Java SDK to build your own
HiveMQ’s flexible and scalable architecture is built to address the unique challenges of smart manufacturing by seamlessly connecting data from edge devices to cloud and enterprise systems. It enables seamless edge data integration by converting industrial protocols into standardized MQTT for an interoperable IIoT infrastructure, provides an enterprise-grade MQTT backbone for scalable data streaming, unifies IT and OT systems with a single source of truth for reliable, real-time decision-making, and transforms data in flight to ensure only relevant, contextualized information reaches cloud and enterprise systems.
A Unified Namespace (UNS) is a modern architectural approach that collects data from across your industrial IoT (IIoT) systems, adds context, and structures it so that other systems and teams can easily access and understand. By creating a centralized, real-time source of truth, a UNS unlocks powerful business outcomes:
Get AI-ready with structured, contextual data
Accelerate digital initiatives by breaking down data silos
Optimize operations with real-time, cross-system visibility
Reduce integration costs with a scalable, standards-based architecture
Unlock AI success in manufacturing. Start with the right data foundation. Discover how to future-proof your operations and drive smarter decisions.
Industrial IoT data streaming unlocks continuous intelligence with AI/ML, driving smarter decisions, better performance, and real-time insights.
Discover how Unified Namespace with MQTT and WinCC OA enables seamless OT/IT integration, real-time data flow, and structured industrial data modeling.
Discover how real-time dashboards and industrial IoT data streaming enable instant insights, faster decisions, and smarter operations across manufacturing.
Discover how to implement IIoT data streaming in smart manufacturing with this practical guide covering key stages, benefits, and insights.
Learn how MQTT enables scalable, real-time industrial IoT data streaming with event-driven architecture and publish-subscribe patterns for smart manufacturing.
Choose between a fully-managed cloud or self-managed platform. Our experts can help you with your solution and demonstrate HiveMQ in action.